Dicing
Providing High-Quality Cutting
with Optimal Processing Technology
The dicing process is essential for making chips from wafers. We have experience in launching single cut, step cut, and other special cut specifications depending on the wafer situation and design requirements. All the machines used for dicing are 2-axis machines. We select the optimum blade and conditions for each wafer, and utilize dicing processing that suppresses chipping as a basic technology.
For SiC, alumina ceramic, and WF with metal film, we use laser dicing equipment to cut high quality.
We also accept dicing prototypes from a single wafer. Please feel free to contact us.
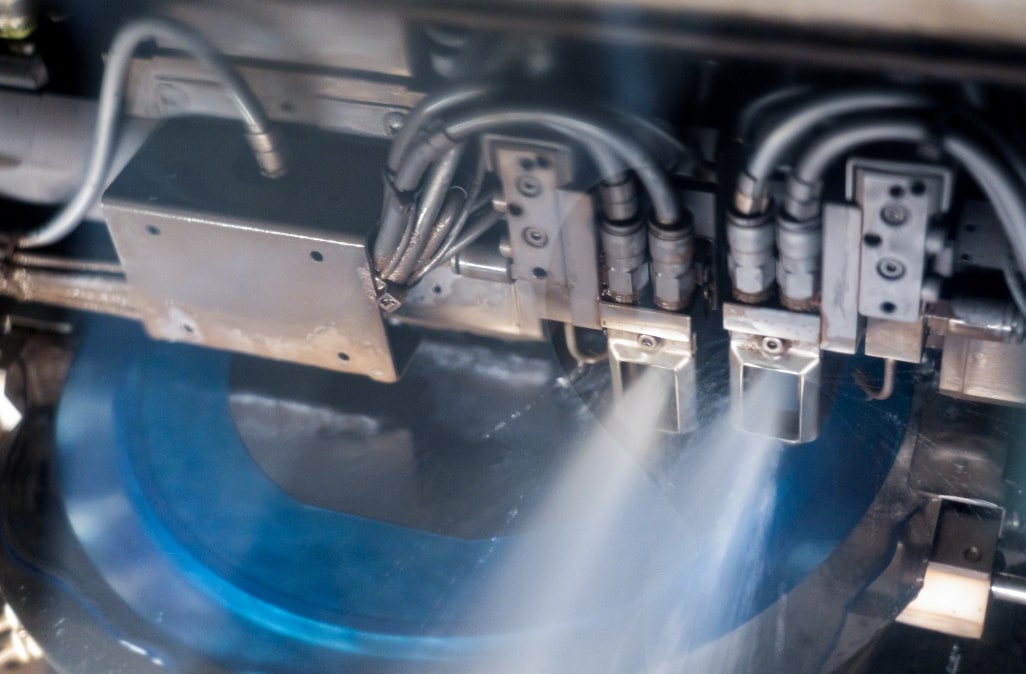
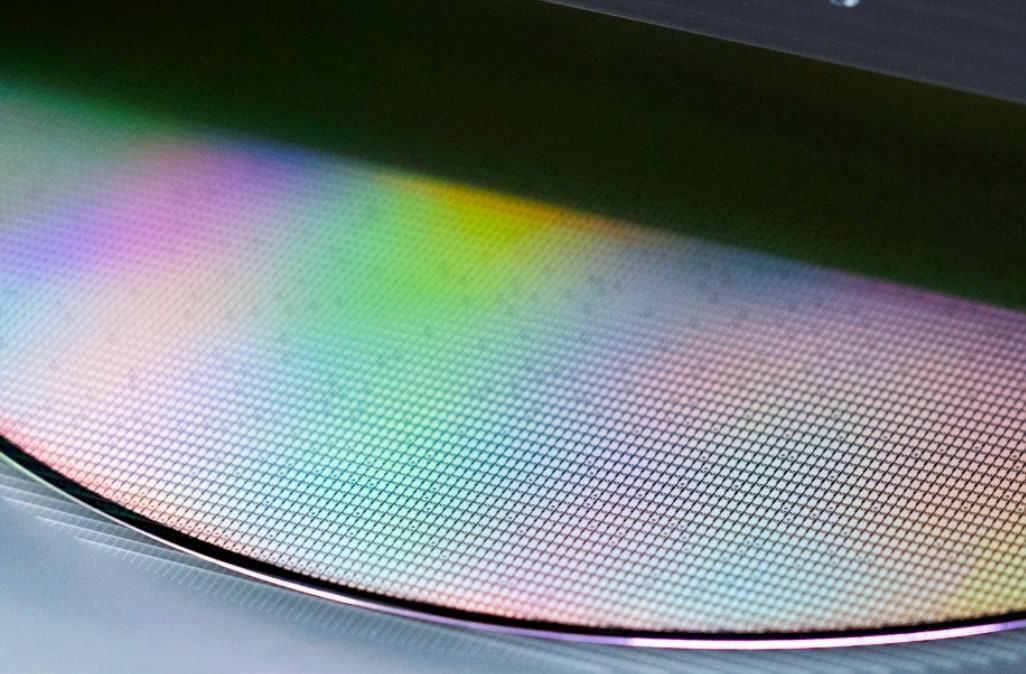
The mounted wafer on the tape is sawn into dice by the cutting wheel with diamond blade that rotates at a high speed. Ultrapure water is poured onto the blade and the wafer, for the sawing performance.
Dicing
Features
01
Feature 1 Advanced Processing Technology
Various Applications
-
Glasses
Alkaline-Free Glasses, Tempax Glasses, Borosilicate Glasses, Sapphire Glasses, Blue Plate Glasses, etc.
-
Ceramics
Alumina, Silicon Nitride, SiC, etc.
-
Silicon
Patterned, Mirror Wafer, etc.
-
Others
Glass Epoxy, Polycarbonate, Acrylic, Various Metals (SUS, etc.), Rubber, etc.
Various Applications
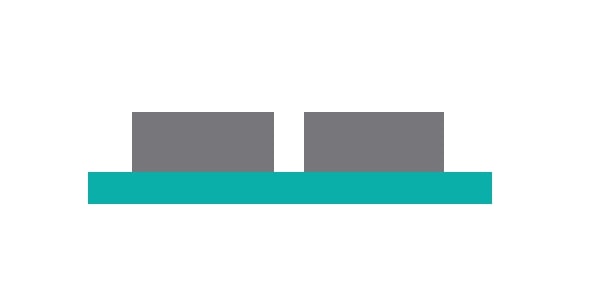
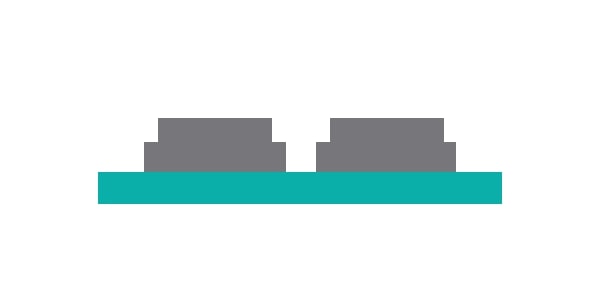
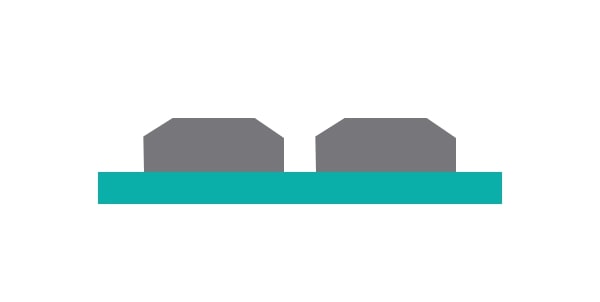
Laser Cut
We cut SiC, alumina ceramic,
and wafers with metal film in high quality with using the laser saw.
Wafer Size/Thickness/Chipping size
-
Applications
·Silicon ・Compound Semiconductors ·Ceramic
・Various Glasses ・Resin (Glass Epoxy, etc.) -
Difficult to Process
・Thick Metal Plates (some can be partially processed, such as thin films)
* However, there is a possibility that it can be cut with laser (at an external partner company) -
Wafer Size
・Diameter 300mm or less
-
Wafer Thickness
・2 mm or less (however, depending on the type of workpiece)
02
Feature 2 High Quality Processing Technology
1
Processing Technology That Eliminates Chipping and Various Scribing Widths Acceptable
We have the know-how to prevent chipping, so we can cut ceramics and glass without chipping.
Improvement Examples of Chipping
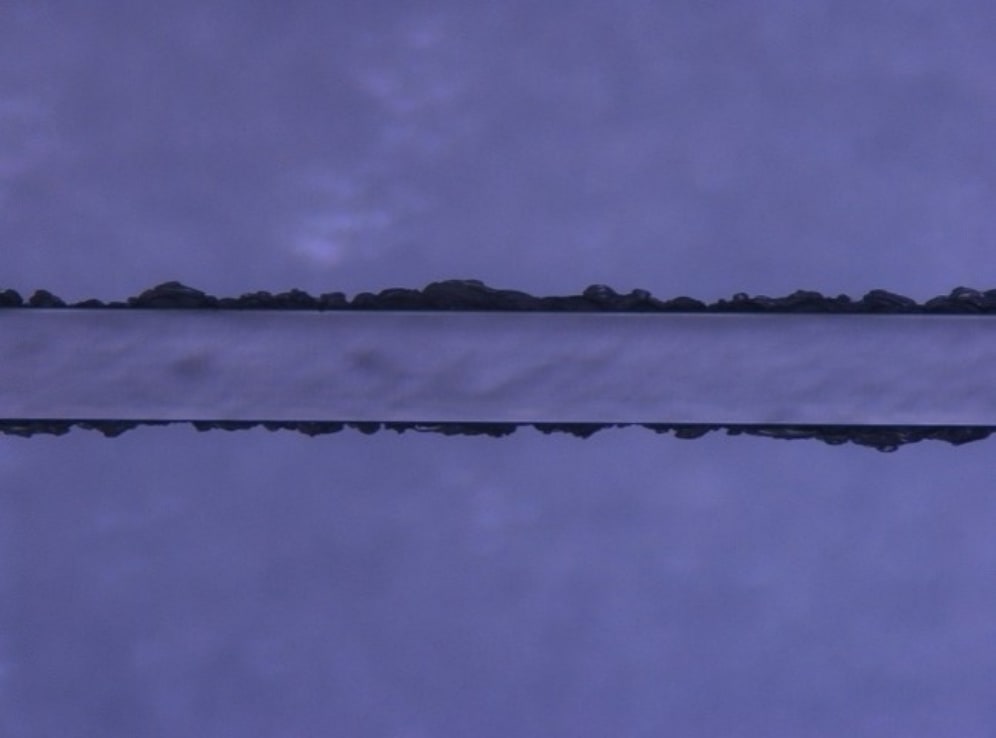
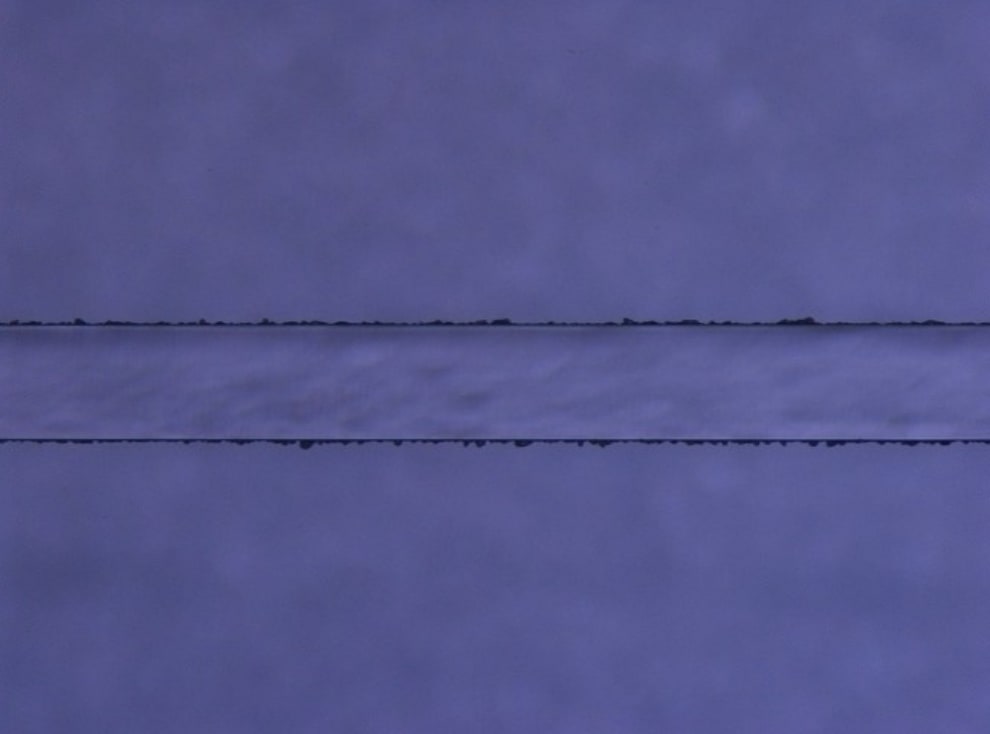
2
Various Scribing Widths Acceptable
Dicing is possible, from a wide scribing width (150 μm ) to a narrow scribing width (40 μm), by various blades and conditions. Chipping on the backside does not happen by means of Step Cut.
3
Prevention of Aluminum Pad Corrosion
During the Dicing process, there is a risk that Aluminum pad corrosion may happen, because sawing is carried out, with DI water poured continuously. Nichiwa Kogyo has the technical know-how that can eliminate various types of corrosion and stain, by improving sawing conditions and DI water.
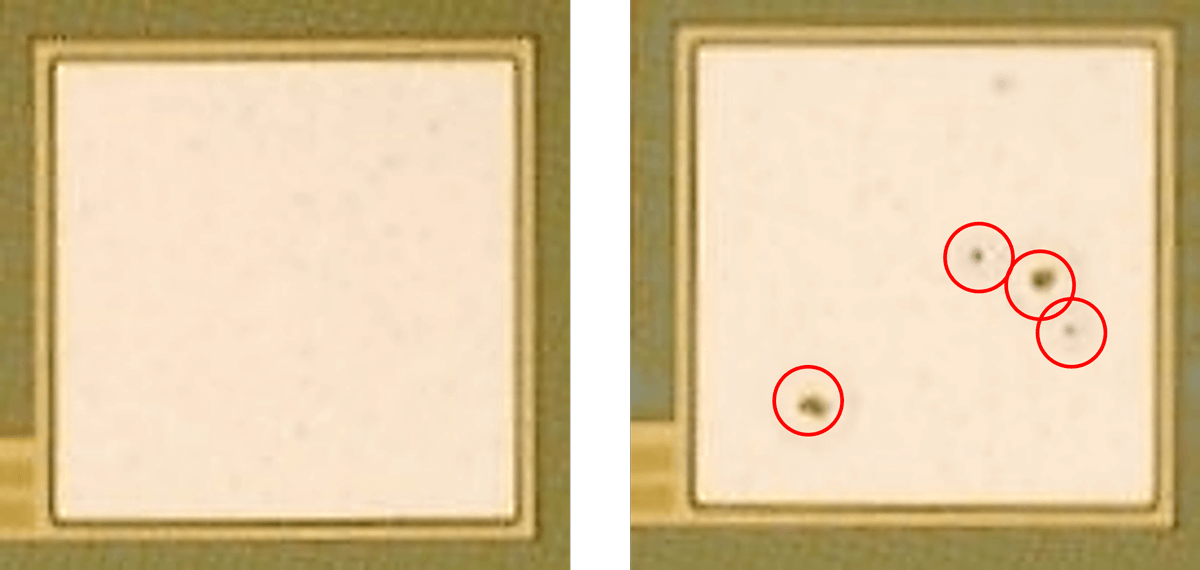
4
High Dimensional Accuracy
We provide highly accurate dicing processing to meet customer requirements.
- Dicing Cut Line Accuracy: ±3 μm
- Dicing Chipping Width: 10 μm or less
03
Feature 3 Available from 1 Piece
Dicing Proccess
We accept orders for dicing from one piece.
We have experience and know-how in processing various materials, so please feel free to contact us.
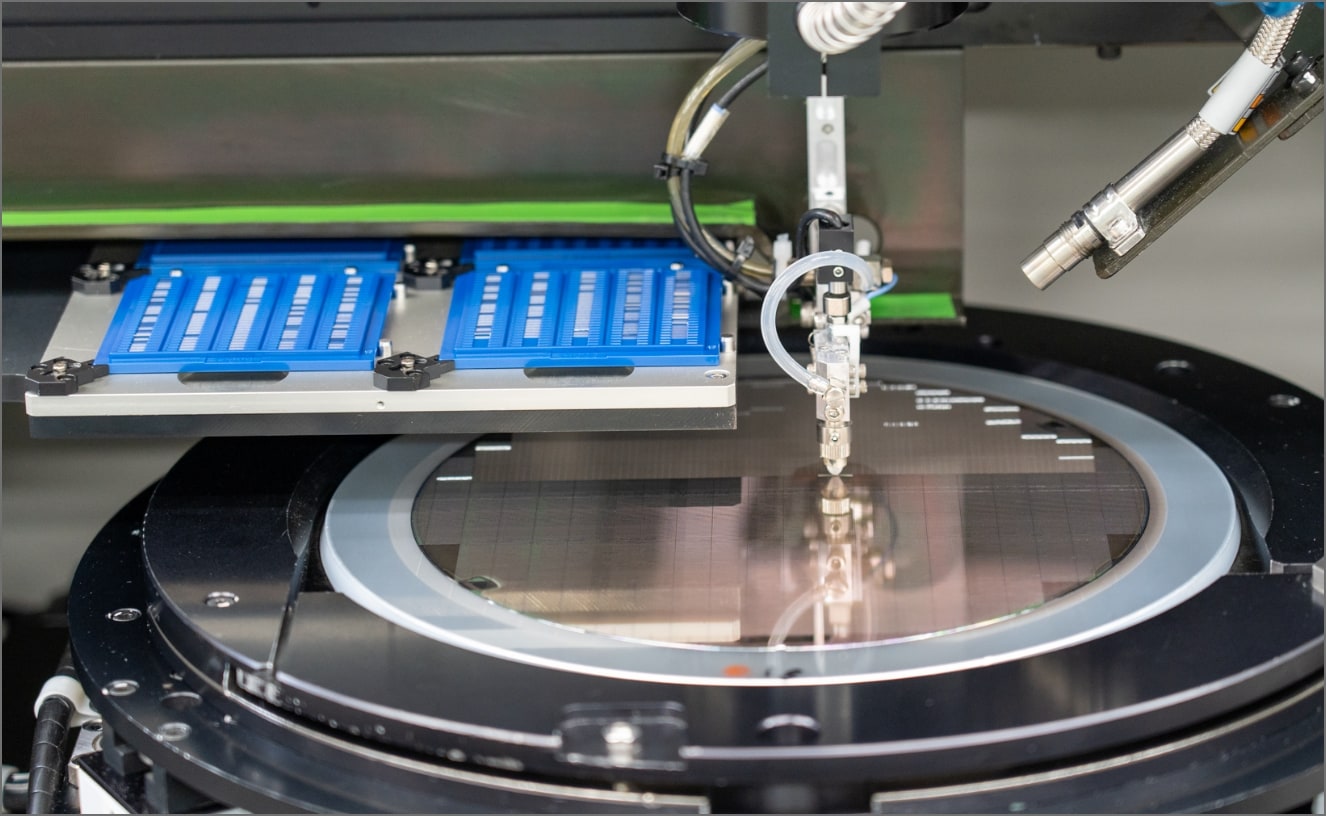
Laser Dicing
We cut SiC, alumina ceramic,
and wafers with metal film in high quality with using the laser saw.
Unlike conventional laser processing, there is no need for focusing and processing can be performed with parallel beams.
In addition, the laser micro jet efficiently cools the workpiece with a constantly flowing water jet, which can suppress thermal effects.
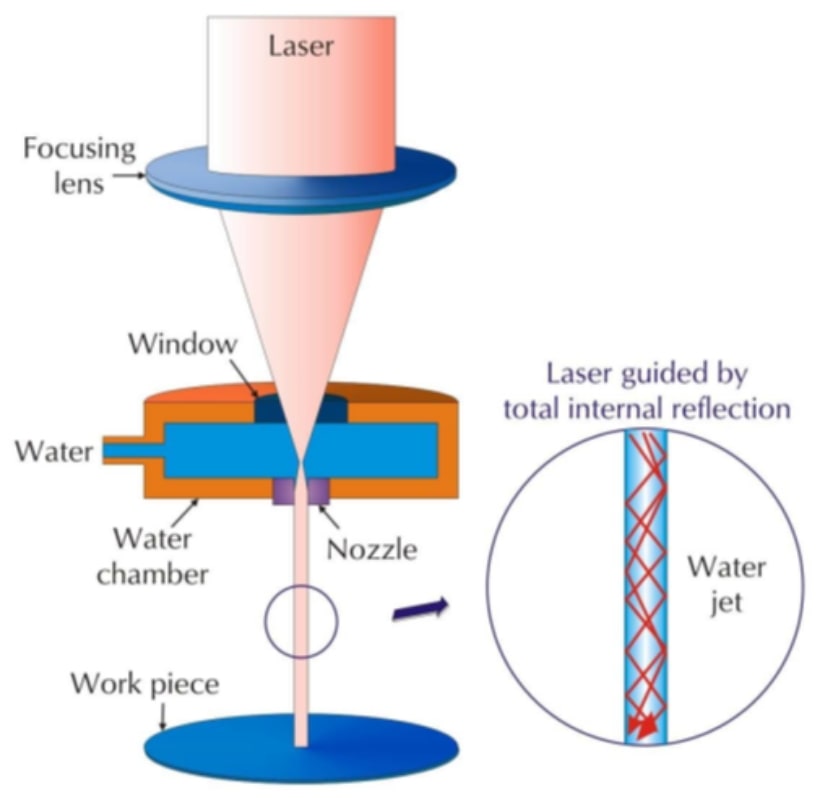
Equipment
Equipment | Wafer Size | Processing Width (Nozzle diameter ≒ Processing Width) |
Number |
---|---|---|---|
Laser Sawer | 4 – 8 inch | 30、40、50、60、70、80、100μm | 1 |
Suitable for Wafers with Back Metals
By processing the front surface with a blade and processing the back metal with a laser micro jet, the occurrence of burrs on the metal can be greatly suppressed.
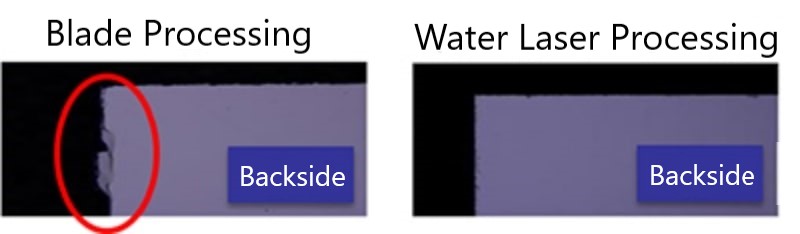